催化燃烧是把有机废气加热到启燃温度,在催化剂的作用下进行无焰燃烧,生成二氧化碳和水并释放大量热量。
2.2.1催化剂的选择
催化燃烧催化剂为固体催化剂,由载体、涂层和活性组分三部分组成。下面就从这三个方面分别加以阐述。
(1)载体
载体除了分散活性组分,也具有调节催化性能的作用。尤其是载体表面的酸性中心具有活化VOCs的作用。
由于A12O3比表面大,且具有催化作用所需要的孔结构,因此被广泛用作各类催化剂的载体。但是,氧化铝存在压力降和热容大、耐热性差、强度低并易破碎等缺点,而且在高温环境下,会转变成热力学上稳定的α-Al2O3,从而导致催化剂活性下降。此外A12O3容易与过渡金属组分生成铝酸盐,这也是目前很难克服的问题。
金属合金载体是70年代末出现的,主要有FeCrAl、NiCr和FeMow等三类合金。从加工和经济价值等综合考虑,FeCrAl是最有应用前景的合金。大量的研究表明,FeCrAl合金具有较好的高温抗氧化性,主要是由于在其表面可选择地形成A12O3膜。金属合金载体的优点为:几何表面积大和较好的几何结构,有利于催化活性物质的吸附;压力降、热容小;具有良好的导热性;机械强度高。主要缺点是载体与涂层材料的膨胀系数差异较大,在使用过程中,由于温度的不断变化,二者之可将产生较大的应力,从而使涂层脱落,缩短催化剂的使用寿命。
随着催化剂对活性组分的分散度、热稳定性的要求不断提高,人们逐渐倾向于选用整体型载体,因其常被制成蜂窝状,故又称为蜂窝载体。堇青石蜂窝陶瓷载体(2MgO·2Al2O3·5SiO2),主要由高岭土(A12O3·2SiO2·2H2O)、滑石(3MgO·4SiO2·H2O)和有机粘台剂挤压成型,干燥后再经过高温焙烧制成。由于堇青石蜂窝陶瓷具有热膨胀系数小(1.8×10-6/℃)、耐热性好等特性,适合作燃烧催化剂的载体。研究表明堇青石具有很高的热稳定性,蜂窝状结构材料具有流体阻力低和气流分布均匀的特点。因此堇青石蜂窝状载体是一种有效、廉价的气体分布器和催化剂载体。如下为蜂窝状载体结构示意图。
蜂窝状载体结构示意图
(2)涂层
由于蜂窝状堇青石载体是经高温焙烧制得,存在着比表面积小、表面平滑难于固定催化剂活性组分等缺点。因此必须寻求一个在较宽的温度范围内物理化学性质较为稳定、且具有高比表面积的物质作为蜂窝陶瓷的涂层。在整体式催化剂中,陶瓷蜂窝载体只是支撑体,涂层才是催化活性组分的真实载体,又称为陶瓷蜂窝载体催化剂的“第二载体”,所以涂层在催化剂的制备中占有举足轻重的地位,也是影响催化剂寿命及催化活性的重要因素。对于涂层,应该具备以下三个条件:1)与陶瓷蜂窝载体之间的粘结强度高;2)对活性组分的吸附性能好:3)热稳定性好。
传统的γ-Al2O3涂层具有比表面大,易吸附活性组分(H2PdCl4、H2PtCl6等)等优点,因此得到了普遍的应用,是最常用的蜂窝陶瓷涂层。但是由于γ-Al2O3在高温环境下容易发生相变,转变成热力学上稳定的α-Al2O3,引起比表面积的大幅度减小,使得催化剂的活性降低;而且在高温下,涂层容易发生烧结,并且出现裂缝和脱落现象。为改善氧化铝的热稳定性,人们通过添加La2O3、BaO、CeO2基复合氧化物等以抑制氧化铝的烧结及相变。
鉴于γ-A12O3涂层的缺点,人们已经将目光转移到研究新的更合适的VOCs催化剂涂层材料上,如SiO2、TiO2、YSZ(Y稳定的ZrO2)、SnO2、La2O3等。
(3)活性组分
活性组分是整体式催化剂最核心的组成部分,直接影响催化效果。活性组分有两类:一类是贵金属,如Pt、Pd、Rh等;另一类是非贵金属,如Cu、Cr、Mn等。根据催化剂所使用的活性组分,可将催化剂分为贵金属催化剂和非贵金属催化剂。
元素周期表中过渡族元素及第Ⅷ族元素中的贵金属具有催化氧化的性能,它们及其氧化物常被用作催化燃烧催化剂的活性成分,例如钛、钒、锰、铁、钴、镍、铜、锌的氧化物及铂、钯、钌等。目前国内催化剂可分为贵金属催化剂、复合氧化物催化剂、稀土元素氧化物等三类。贵金属催化剂起燃温度低,资源稀少,价格昂贵,易中毒;复合氧化物催化剂降低了成本,清除效果也很好;稀土元素氧化物具有助催化作用,能提高催化活性及热稳定性。
目前用得最多的是Pt和Pd两种。贵金属催化剂的初始活性很好,主要表现如下:启燃温度低、完全燃烧温度与启燃温度相差很小,即活性随温度上升很快。而且由于Pt和Pd能负载在比表面积相当大的载体上,且能高度分散,所以仅用少量贵金属(0.1-0.5wt%)就可以达到好的催化活性。但这类催化剂也存在一些缺点,主要是价格高、资源有限等。一般认为,贵金属催化剂的高活性与活化H2、O2、C-H和O-H键的能力有关联。对于负载型Pd催化剂的失活原因,一般认为有以下几种:载体(如γ-Al2O3)烧结,形成尖晶石;Pd或者PdO烧结及PdO的分解(PdO→Pd+1/2O2)。
与贵金属催化剂相比,过渡金属催化剂的性能主要表现在:启燃温度比贵金属催化剂高;完全燃烧温度(T90%)与启燃温度(T10%)相差很大,即活性随温度升高上升缓慢。有些催化剂的启燃温度虽然低,但是完全燃烧温度却较高。尽管目前过渡金属氧化物催化剂的热稳定性取得了较大的提高,但是主要问题仍然没有解决。用于VOCs催化燃烧催化剂的非贵金属一般都是化学元素周期表中第四周期的Cr、Mn、Fe、Co、Cu等元素的氧化物。目前研究最多的非贵金属催化剂主要是钙钛矿型催化剂。钙钛矿催化剂都具有钙钛矿(分子式为ABO3)结构。A多为La,B多为Fe、Co、Mn等过渡金属。
催化燃烧催化剂会发生中毒现象。为防止催化剂中毒,可在废气进入反应器前设废气预处理装置,清除废气中粉尘和毒物,并定期进行再生和清洗等。导致催化剂中毒的毒物(抑制剂)主要有磷、铅、秘、砷、锡、汞、亚铁离子、锌、卤素等。
催化热破坏处理设备能达到的有机物热破坏效率在90~95%之间,稍低于直接火焰燃烧,这是由于废气停留在催化床层填料或催化材料涂层的时间长,降低了催化剂有效表面积从而降低了全面破坏效率。催化剂常只针对特定类型化合物反应,所以催化燃烧的应用在一定程度上受到限制。
2.1.2催化燃烧系统
催化燃烧室采用蜂窝陶瓷状为载体的贵金属催化剂,阻力小,活性高。当有机蒸气浓度达到2000ppm以上时,可维持自燃。贵金属蜂窝状陶瓷载体催化剂比表面积大。余热可回用:余热可返回烘道,降低原烘道中消耗功率,也可作其它方面的热源。催化燃烧技术要求有机废气具有足够高的热值,限制了低浓度(500~2000mg/h3)有机废气处理方面的应用。流向变换催化燃烧技术结合了蓄热燃烧和催化燃烧的特点,可适用的有机废气浓度范围较常规催化燃烧技术更低,减少辅助燃料的投资,经济性良好。
反应塔内装填特制的固态复合填料,填料内部复合催化剂。当废气在引风机的作用下穿过填料层,与通过特制喷嘴化剂在固相填料表面充分接触,并在催化剂的催化作用下,恶臭气体中的污染因子被充分分解。工艺部分主要有催化室、电加热箱、热交换器、风机、电控柜五大部分组成。
催化燃烧装置示意图
当有机废气进入装置先到热交换器,用催化燃烧后的余热通过热交换器把有机废气温度尽可能的提高,通常升温△t=50-60℃,然后送入电加热箱内,通过电热管加热到启燃温度,一般在200-250℃。达到温度会自动关闭加热系统,这时就进入催化箱内,进行催化燃烧反应,是有机废气氧化分解成二氧化碳和水,并且释放大量的热量。当有机废气浓度一定量时,产生的余热通过热交换器后升温达到启燃温度,这时催化燃烧装置就达到动态热平衡,大量节省了电功率。
2.1.3催化燃烧催化剂评价体系
催化燃烧装置就是把有机废气预热到启燃温度,在催化剂的作用下生成无毒的二氧化碳和水,放出大量的热。催化剂的性能主要参数为:启燃温度、空速指标、抗中毒功能及使用寿命。启燃温度直接影响能耗;空速指标反映催化剂的承受风量指标;抗中毒主要对有毒元素达到一定量的指数,使用寿命反映在同等条件下的使用寿命年限。
催化活性测试在常压微型固定床反应器中进行,催化剂用量约300mg。反应气组成(体积百分比):(1)对于用浸渍法和共沉淀法制备的样品CH41%,O220%,N279%,空速50000ml/g.h。(2)对于用溶胶-凝胶法制备的样品CH44%,O217%,其余为N279%,空速6.0×104ml/g.h。反应产物用气相色谱仪在线分析,氢火焰(FID)检测,柱温80℃,Y5分子筛分离柱,柱长2m。催化剂活性用甲烷转化率在10%,50%和90%时所对应的温度T10%,T50%和T90%表示。其中T10%定义为甲烷催化燃烧的启燃温度。
具体操作:准确称取定量的催化剂和等量的石英砂,均匀混合后装入直径为Φ=8mm的石英管微型反应器中,催化材料床层高度20mm。通入反应气一定时间达到平衡后,再以4℃/min速度进行程序升温,考察200-820℃之间不同温度下的甲烷燃烧催化活性。
催化材料活性评价流程图
1质量流量计;2混合器;3带加热炉的固定床微型反应器;4温控仪;5热电偶;6除水器;7六通阀;8气相色谱;9数据处理系统
2.1.4催化燃烧法特点
催化燃烧法具有如下特点:催化燃烧为无火焰燃烧,安全性好;要求的燃烧温度低,大部分烃类和CO在300-450℃之间即可完成反应,辅助燃料消耗少;对可燃组分浓度和热值限制较小;对疏水性污染物质有很好的去除率;耐冲击负荷,不易被污染物浓度及温度变化影响;为使催化剂延长使用寿命,不允许废气中含有尘粒和雾滴。
优点:一般情况下去除率均在95%以上。
缺点:(1)适合于处理浓度较高的VOCs废气。(2)催化燃烧法降低了燃烧费用,但催化剂容易中毒,对进气成份要求极为严格,同时催化剂需要定期更换,废弃的催化剂如何处理还有待进一步研究,而且一种催化剂一般只对某一特定类型的有机物有效,如果处理混合型的VOCs废气,则需要多种不同类型的催化剂,此外由于催化剂成本很高,使得该法处理费用大大提高。(3)废气中的VOCs不完全燃烧有可能产生比初始气体更有害的污染物,如乙醛,二恶英,呋喃等。(4)不适于处理燃烧过程中产生大量硫氧化物和氮氧化物的废气。
一次免费学习与交流的机会,扫码在线预约,你值得拥有!欢迎关注“2018 第五届重点行业有机废气(VOCs)污染治理及监测技术交流会”。
时间:2018年5月4日
地点:上海 新国际博览中心 会议区E6-6271
扫码报名,免费参加“2018 第五届重点行业有机废气(VOCs)污染治理及监测技术交流会”
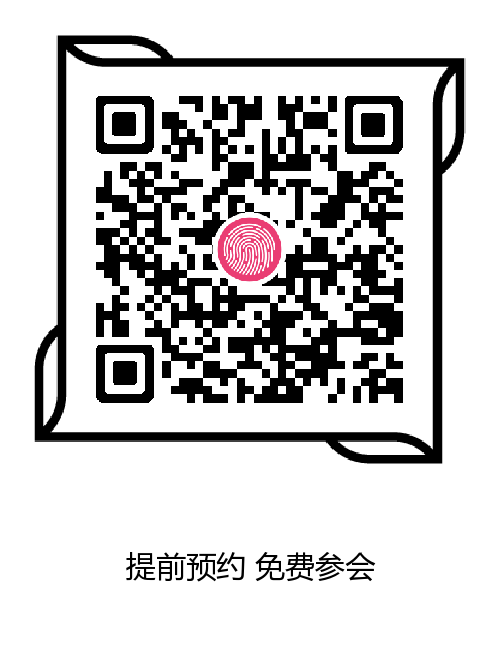
更多你可能感兴趣的内容
政策解读
|
《“十三五”挥发性有机物污染防治工作方案》解读及重点行业VOCs 污染防策研究
|
环境保护部环境规划院,大气部大气综合规划室主任、研究员 宁淼
|
VOCs排放控制方式与技术要点
|
环保部环境标准研究所研究员 张国宁
|
化工园区
|
化工园区绿色发展与VOCs治理需求
|
中国石油和化学工业联合会 化工园区工作委员会处长 马从越
|
全在线双冷阱大气预浓缩常规四级杆气质VOCs监测系统
|
上海炫一电气有限公司 总经理 张彦俊
|
化工园区VOCs在线连续监测系统解决方案
|
北京京仪集团有限责任公司所属北分麦哈克 技术总监 陈淼
|
工业涂装行业
|
工业涂装行业VOCs综合治理路线选择及工程设计
|
上海机电设计研究院 高级工程师 李磊
|
制药行业
|
用分子筛处理制药发酵尾气
|
河北莫兰斯环境科技股份有限公司 副总经理 姚振永
|
包装印刷行业
|
VOCs末端治理技术节能型旋转RTO整体解决方案
|
西安昱昌环境科技有限公司 总经理 任玲辉
|
VOCs治理技术应用及研究
|
利用沸石转轮技术优化VOC减排过程及产品适用性分析
|
蒙特中国 VOC行业总监 计成飞
|
华世洁VOCs治理核心工艺价值共享
|
青岛华世洁环保科技有限公司 营销总经理 隋宝玉
|
装卸、储运过程VOCs废气回收关键技术及安全防爆措施解析
|
原中国石化上海高桥石油化工有限公司 VOCs治理行业专家 邹松林
|
VOCs治理技术问题解析开放讨论
|
l VOCs治理技术“痛点”解析(活性炭吸附、燃烧法、生物法、光催化氧化、低温等离子法)
l VOCs无组织排放控制技术解析(设备与管件泄露、敞开液面逸散、挥发性有机液体储运与装载、以VOCs为原料的生产全过程、涂装、印刷等)
l VOCs之LDAR技术解析(设备种类相关性)
l VOCs安全运维与设备防爆解析
|
会务联系
赵先生:010-65812031 13581565096
谭先生:010-85804450 18510117105
姜先生:010-56107971 18500471021
龚先生:010-65818146 17600104709
声明:转载此文是出于传递更多信息之目的。若有来源标注错误或侵犯了您的合法权益,请作者持权属证明与本网联系,我们将及时更正、删除,谢谢。

使用微信“扫一扫”功能添加“谷腾环保网”